Сравнительный анализ показателей бетонов для дорожных покрытий: оценка влияния различных видов цемента и нерудных материалов на основные свойства бетона
В статье рассмотрена проблема образования колеи в цементнобетонных покрытиях автомобильных дорог и определены факторы, влияющие на образование данного дорожного дефекта и величину износа при воздействии на него шипованных шин.
Это актуальная проблема, снижающая интенсивность применения и развитие строительства сети автомобильных дорог с цементобетонными покрытиями на территории Российской Федерации. Основной способ повышения стойкости дорожного покрытия к колееобразованию — это требовательный и методичный подход к подбору состава бетона. Группой компаний, входящих в Ассоциацию бетонных дорог, был рассмотрен опыт зарубежных стран, проведены испытания, разработаны предложения по подбору состава цементобетонных смесей для строительства автомобильных дорог с цементнобетоными покрытиями с критериями.
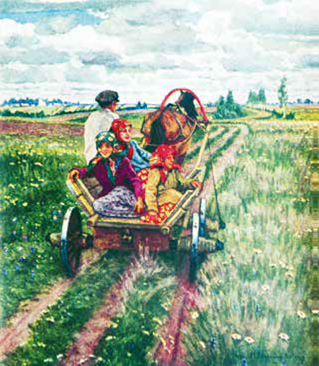
Известное выражение «выбиться из колеи» означает выйти из обычного образа жизни, потерять ее привычный ритм. История этого фразеологизма возвращает нас в то время, когда колеей назывался след от колес на грунтовой дороге. Чем больше транспорта проезжало по этому следу, тем глубже и укатаннее становилась колея. Вследствие этого дорога становилась спокойной, без тряски и неожиданных поворотов: колея мешала. Сейчас «колея» — это изменение поперечного профиля проезжей части в виде продольного углубления по полосе наката. Колея создает высокий риск потери управления автомобилем при следующих обстоятельствах:
- выезд из колеи;
- образование слоя жидкости в колее, что приводит к процессу аквапланирования;
- образование слоя жидкости вследствие применения противогололедных материалов при пониженных температурах, которое приводит к образованию в колее дополнительной скользкости.
Согласно статистике ГИБДД, 20 % ДТП из-за колейности происходят по причине потери управления автомобилем.
Колееобразование является следствием износа дорожного покрытия и представляет собой разрушение покрытия в процессе истираемости колесами автомобиля, а также от ударов колесами. Основной причиной износа является применение автомобилистами шипованных шин на автодорогах.
В скандинавских странах колейность удалось снизить с помощью таких эффективных мер, как:
- внедрение системы управления состоянием дорожной одежды;
- снижение скорости движения в зимний период;
- технический регламент на шипованные шины, в котором количество шипов на одном погонном метре покрышки должно быть не более 50 шт.;
- применение высококачественных заполнителей при проектировании бетонной смеси для автомобильных дорог с цементобетонными покрытиями;
- снижения веса шипов.
К сожалению, в действующих в России нормативных документах износ дорожных покрытий от шипованных шин практически не учитывается. Отсутствуют методики оценки, требования и прогнозирование износостойкости цементобетонных покрытий автомобильных дорог в зависимости от интенсивности движения.
Для определения влияния воздействия шипованных шин на цементобетонное покрытие группой компаний, входящих в Ассоциацию бетонных дорог, были проведены натурные испытания на универсальном комплексе «Карусель» Учебно-научного центра МАДИ. Основная задача испытаний — оценка стойкости цементобетонного покрытия к образованию колеи при воздействии шипованных шин в зависимости от состава бетона.
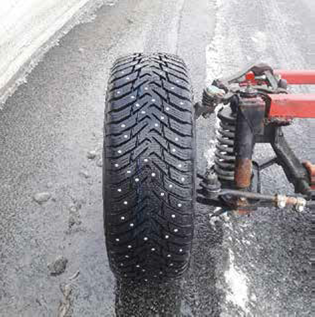
Для выполнения исследований установку «Карусель» оснастили колесами радиусом 16 дюймов с количеством шипов 90 штук на погонный метр. Линейная скорость колеса при проведении испытаний была равна 85 км/ч при нагрузке в 550 кг.
На стенде была изготовлена полоса наката из цементобетонных плит. Бетонные смеси и бетоны подбирались согласно своду правил «Автомобильные дороги» СП 34.13330.2012. Дорожные покрытия из цементобетона должны соответствовать минимальным проектным требованиям бетона классов В30, Btb 4,0. По технологии строительства цементобетонных дорог с применением дорожных бетоноукладчиков требуемый класс удобоукладываемости бетонной смеси соответствовал П1. Для обеспечения высоких эксплуатационных характеристик был назначен высокий класс бетона по истираемости G1 (ГОСТ 13015-2012 п. 5.6.11 «Изделия бетонные и железобетонные для строительства. Правила приемки, маркировки, транспортирования и хранения»), по морозостойкости — F2 300.
Основная задача исследования заключалась в подборе наилучшего для эксплуатации состава бетонной смеси на основе различных цементов и крупных заполнителей с обеспечением свойств заданного качества. В исследовании использовались три типа цемента и три типа щебня различных фракций. В табл. 1 представлены основные технические показатели использованных типов цемента и щебня.
Таблица 1. Показатели использованных в испытании типов цемента и щебня
Производитель / Показатель | Щуровский ЦЗ ГОСТ 31108 | Щуровский ЦЗ ГОСТ 10178 | Мальцовский ЦЗ ГОСТ 10178 |
---|---|---|---|
Тип цемента | ЦЕМ I 42.5Н | ПЦ 500-Д0-Н | ПЦ 500-Д0-Н |
Удельная поверхность, см²/г | 3335 | 3440 | 3102 |
Нормальная густота цементного теста, % | 27,2 | 27,4 | 25,4 |
Предел прочности при изгибе 2 суток, МПа | 4,5 | — | — |
Предел прочности при сжатии 2 суток, МПа | 21,3 | — | — |
Предел прочности при изгибе 3 суток, МПа | — | 4,8 | 4,8 |
Предел прочности при сжатии 3 суток, МПа | — | 36,6 | 34,4 |
Предел прочности при изгибе 28 суток, МПа | 9,0 | 6,7 | 7,2 |
Предел прочности при сжатии 28 суток, МПа | 53,4 | 59,6 | 53,5 |
Применяемый цемент по всем показателям соответствовал заданным требованиям ГОСТ 30515-2013 «Цемент. Общие технические условия».
В исследовании использовался песок Мансуровского карьероуправления, выпускаемый по техническим условиям ГОСТ 8736. Песок и соответствует показателям песка первого класса, средней группы. Но для автомобильных дорог общего пользования песок должен соответствовать ТР ТС 014/2011 и ГОСТ 32824 «Дороги автомобильные общего пользования. Технические требования. Песок природный», поэтому песок был дополнительно испытан на соответствие этим стандартам.
Результаты испытаний на соответствие ГОСТ 32824-2014 приведены в табл. 2. Отклонение по содержанию зерен крупностью менее 0,125 мм посчитали незначительным. Большее влияние оказывает гравийная составляющая в песке. По терминологии ГОСТ 8736 песок — это «неорганический сыпучий материал с крупностью зерен до 5 мм». Согласно стандарту «Заполнители для бетона» DIN EN 12620 песком считается каменный материал с размером зерен до 2 мм. Такая разница имеет значение в требованиях к заполнителям для специального бетона, к которому и относится бетон для верхнего дорожного слоя. Однако в стандартах РФ дополнительных требований нет.
Таблица 2. Результаты испытаний на соответствие ГОСТу 32824-2014 песка Мансуровского карьероуправления
Показатель |
Требования ГОСТа 32824-2014. Дороги автомобильные общего пользования |
Фактическое значение |
---|---|---|
Модуль крупности (группа) песка | Св. 2,3 до 2,8 вкл. | 2,7 (средний) |
Класс песка | I | II (по гран. составу ост. менее 0,125) |
Полный остаток на сите 0.5 мм | От 40 до 55% | 51,2 |
Содержание зерен крупностью > 8 мм, % | 0,5 | 0 |
Содержание зерен крупностью > 4 мм, % | 5,0 | 5,0 |
Содержание зерен крупностью < 0.125 мм, % | 3,5 | 4,5 |
Содержание пылевидных и глинистых частиц, % | 2 | 1,6 |
Истинная плотность, г/см3 | — | 2,66 |
Пустотность, % | — | 40,7 |
Слабые зерна карбонатных пород, содержащиеся в песке в виде гравия с зернами размером более 2 мм, снижают эксплуатационную стойкость покрытия при воздействии шипов. Поэтому песок для верхнего слоя не должен содержать гравия.
Для дорожного покрытия верхнего слоя требуется использовать более прочные и устойчивые горные породы. К ним, например, относится порфирит – Rсж до 300 МПа. Это горная вулканическая порода, в составе которой отсутствует кварц. Порфирит имеет скрытокристаллическую структуру, зерна не различимы простым глазом. Порода не разрушается, не дает трещин и сколов, устойчива при частых изменениях температуры в широком диапазоне, кислотоупорна. Для проведения испытаний был выбран щебень из порфирита, фракция 5–25 мм, карьер ОАО «Порфирит», пос. Березовка, республика Карелия.
В группу устойчивых пород также входит габбро-диабаз — Rсж до 300 МПа, обладает высокой твердостью и прочностью, более морозо- и влагоустойчив. Для испытаний использовался щебень из габбро-диабаза в виде двух широких фракций 5–10 и 10–20 мм, добытый из карьера «Голодай Гора», ООО «Лафарж Нерудные Материалы и Бетон», пос. Деревянка, республика Карелия.
Дополнительный щебень из габбро-диабаза фракции 4–8 произведен из сырья карьера «Голодай Гора» иным методом — электрогидравлическим дроблением. Раскалывание материала осуществляется ударной волной — квазигидростатическим давлением, возникающим в объеме жидкости. При этом типе дробления щебень имеет правильную кубовидную форму, а дробление происходит с меньшим количеством отходов и пыли.
Граниты образуются из магм кислого состава (SiО2 более 60 %). Главными породообразующими минералами являются кварц, калиевые полевые шпаты, кислые плагиоклазы и биотит (иногда мусковит и роговая обманка). Прочность породы — Rсж до 250 МПа. Использовался щебень фракции 5–20 (производитель Украина).
Таблица 3. Сводная таблица основных характеристик крупного заполнителя-щебня.
Показатели качества по ГОСТу 32703. Дороги автомобильные общего пользования
Маркировка крупного заполнителя | Проход через контрольные сита | Насыпная плотность в воздушно-сухом состоянии | Средняя плотность зерен | Содержание зерен пластинчатой и игловатой формы | Пустотность | Дробимость в сухом состоянии до 9% - D1400 | Дробимость в насыщенном состоянии до 9% - D1400 | Водопоглощение |
---|---|---|---|---|---|---|---|---|
Единица измерения | Марка | т/м³ | г/см³ | % | % | % | % | % |
Габбро-диабаз фракций 5-10 мм | 85/15 | 1,64 | 2,97 | 1,99 | 44,8 | 1,99 | 2,38 | 0,86 |
Габбро-диабаз фракций 10-20 мм | 85/15 | 1,71 | 2,98 | 5,51 | 42,6 | 5,51 | 6,57 | 0,57 |
Габбро-диабаз ЭГД фракций 4-8 мм | 90/15 | 1,69 | 2,97 | нет | 43,0 | 2,20 | 3,40 | 1,6 |
Гранит фракции 5-20 мм | 90/10 | 1,55 | 2,67 | 9,1 | 41,9 | 5,30 | 7,24 | 0,89 |
Порфирит фракция 5-15 мм | 90/10 | 1,58 | 2,90 | 2,30 | 45,5 | 2,30 | 2,98 | 0,84 |
Щебням присвоены марки по гранулометрическому составу. По средней плотности зерна – от тяжелого к легкому — следуют габбро-диабаз, порфирит и гранит. По содержанию зерен c пластинчатой формы все щебни классифицируются маркой Л10, т. е. не более 10 %.
Самые сильные разрушения строительных материалов происходят в водонасыщенном состоянии. Вода увеличивает энергию воздействующих сил износа на разрушение материала из-за расклинивающего давления, образующегося в микротрещинах. Поэтому для использования заполнителя в верхнем слое дорожной одежды все свойства, отвечающие за долговечность, должны определяться в водонасыщенном состоянии, а для определения параметров — в сухом состоянии. Результаты двух испытаний должны быть в значениях одного класса технических условий. Результаты, полученные при испытании исследуемых щебней, в сухом и в насыщенном состоянии находились в рамках одного класса.
В соответствии с ГОСТ 26633 «Технические требования», п. 4.7.13 «при проектных требованиях к бетону марки по морозостойкости F2 100 и выше должен применяться крупный заполнитель из изверженных и метаморфических пород с водопоглощением не более 1,0 %».
Согласно исследованию финских ученых, которое приводят специалисты «Стройпроекта», способность цементобетонного покрытия сопротивляться воздействию шипованных шин на 60 % зависит от качества щебня. Показатель сопротивления дроблению и износу определяется по ГОСТ 33049 («Дороги автомобильные общего пользования»). В технических требованиях ГОСТ 32703 щебень подразделяется на 6 марок. Метод испытаний аналогичен старому ГОСТу (ГОСТ 8269), изменились только требования к значениям. Для класса И1 потеря массы в ГОСТ 8267 составляет до 25 %, в ГОСТ 32703 — до 15 %. В требованиях стандарта щебень испытывают в сухом состоянии.
В странах Европейского Союза для дорог с высокой интенсивностью движения используется метод Nord test. Метод является действующим стандартом Республики Беларусь (СТБ ЕN 1097-9-2013). В нем используется барабан d 205x335 с тремя ребрами и высотой 8 мм, а также стальные шарики диаметром 15,0 мм. Для начала готовится проба по фракциям от 11,2 до 14 и от 14 до 16 мм. Затем берется в отношении по фракциям 35/65 и вычисляется масса навески щебня с учетом средней плотности. Пробу около 1 кг помещают в барабан, добавляют необходимое количество стальных шариков до получения массы 7000 г и 2 л воды. Барабан закрывают крышкой и при частоте вращения 90 об./мин совершают 5400 оборотов. После испытаний заполнитель и стальные шарики помещают в емкость, промывают через сита с размером ячеек 14, 8 и 2 мм. Далее сита высушиваются и определяется потеря массы. Согласно финским стандартам, на дорогах с высокой интенсивностью движения может использоваться только щебень, у которого потеря массы после проведения испытания в «шаровой мельнице» не превышала 7 %. Как показали исследования финских специалистов, только 15 % горных пород в Финляндии соответствуют этому требованию.
Описанный метод Nord test значительно отличается от российского метода «Лос-Анджелес»» по интенсивности воздействия на бетон: по количеству и массе материала, по условиям испытания воздушные и водные), по скорости вращения и количеству оборотов. В данной работе для получения приближенных условий к условиям эксплуатации щебень перед испытаниями методом «Лос-Анджелес» испытывали в водонасыщенном состоянии. Результат испытания приведен в табл. 4.
Таблица 4. Результаты испытания различных видов щебня методом «Лос-Анджелес»
Маркировка крупного заполнителя | ГОСТ 33049 Сопротивление износу в водонасыщенном состоянии, % по массе |
СТБ EN 1097-9-2013 Устойчивость к истиранию шипованными шинами |
Марка по истираемости | ||
Единица измерения | % | % |
Габбро-диабаз фракций 10-20 мм |
15,0 И 1 |
8,5 AN10 |
Гранит фракции 5-20 мм |
15,2 И 2 |
6,8 AN7 |
Порфирит фракции 5-15 мм |
7,4 И 1 |
6,4 AN7 |
Из полученных результатов можно сделать следующие выводы: российский метод «Лос-Анджелес» жестче по воздействию на материал, так как потери в нем выше. Но при различных воздействиях разнятся как сопротивление, так и полученные результаты.
Согласно требованиям ГОСТ 26633, водоцементное отношение не должно превышать значения 0,45, а воздухововлечение в верхнем слое покрытия должно быть в пределах 5–7 %.
Составы бетонных смесей были подобраны исходя из обеспечения заданных показателей, а также одинакового количества цемента, равного объема щебня в смеси и водоцементного отношения. Незначительно менялось количество песка в смеси. Все бетоны соответствовали классу по подвижности П1. Для достижения высокого класса по морозостойкости в составах использовалась воздухововлекающая добавка, которая подбиралась индивидуально для каждого состава.
По данным результатов испытаний все бетоны имели требуемые значения для цементнобетонных покрытий. Фактические прочности на сжатие от 45,8 до 54,6 МПа, прочности на растяжение при изгибе — от 4,1 до 5,1 МПа.
В течение испытаний установка работала с ноября по март, в связи с этим для очистки от зимней скользкости применяется противогололедный материал ГРИН ВЭЙ.
В отечественных стандартах не нормируются требования к заполнителю по морозостойкости в зависимости от характеристики среды, указано лишь, что марка заполнителя по морозостойкости должна быть не ниже, чем марка бетона по морозостойкости. В рамках исследовательской работы щебни испытывали параллельно образцам-кубам, аналогичным методом в соответствии с ГОСТ 10060 «Бетоны. Методы определения морозостойкости» (табл. 5).
Таблица 5. Результаты испытаний морозостойкости бетонов и крупных заполнителей
Заполнитель | ГОСТ 10060 третий ускоренный метод | Габбро-диабаз 5-20мм | Габбро-диабаз 4-8 мм | Гранит 5-20 мм | Порфирит 5-15 мм |
---|---|---|---|---|---|
Цемент | |||||
Щуровский ЦЕМ I 42.5Н | Прочность на сжатие контрольных образцов кубов, МПа | 43,5 | 38,0 | — | 43,4 |
Прочность на сжатие основных образцов кубов, МПа | 46,1 | 42,6 | — | 42,7 | |
Xmin2 ≥ 0,9*Xmin1 | МПа | 39,7 ≥ 36,0 | 34,3 ≥ 29,7 | — | 37,5 ≥ 35,5 |
Щуровский ПЦ 500-Д0-Н |
Прочность на сжатие контрольных образцов кубов, МПа | 47,4 | 46,9 | — | 47,3 |
Прочность на сжатие основных образцов кубов, МПа | 51,9 | 49,0 | — | 47,7 | |
Xmin2 ≥ 0,9*Xmin1 | МПа | 45,7 ≥ 36,0 | 44,0 ≥ 36,8 | — | 40,1 ≥ 39,4 |
Мальцовский ПЦ 500-Д0-Н |
Прочность на сжатие контрольных образцов кубов, МПа | — | — | 50,2 | — |
Прочность на сжатие основных образцов кубов, МПа | — | — | 48,9 | — | |
Xmin2 ≥ 0,9*Xmin1 | МПа | — | — | 42,2 ≥ 39,7 | — |
Потери щебня по массе, 37 циклов | до 2 % | 0,69 | 4,48 | 0,57 | 1,02 |
Щебень из Габбро-Диабаза фракции 4–8 мм не прошел испытания: водопоглощение превышало допустимое значение более чем на 1 %. Бетон, в свою очередь, испытания прошел, так как заполнитель находился под защитой «рубашки» из цементного слоя. При воздействии шипов на дорожное покрытие идет разрушение материала, характер разрушения ударно-абразивный, щебень обтачивается по контактной зоне с растворной частью бетона. Как только высота раствора оголяет камень более чем наполовину, шип выбивает щебень из полотна. Это происходит, когда усилие, возникающие при воздействии шипов, сравняется с прочностью сцепления щебня с цементной матрицей. Поэтому для дорог с высокой интенсивностью движения количество щебня должно быть более 50 % по объему, так как это увеличивает площадь камня относительно площади цементного раствора зоны контакта верхнего слоя дорожной одежды. Для этого необходимы узкие фракции, чтобы моделировать гранулометрический состав заполнителей для специальных бетонов. Кроме того, рекомендуется использовать дополнительные способы для увеличения адгезии цементного раствора с зерном щебня.
Заключение и выводы
В процессе исследовательской работы установлено, что для снижения риска возникновения колейности покрытия:
- фракции гравия в песке не должны превышать 2 мм;
- содержание щебня нескольких узких фракций должно составлять М90/10;
- содержание щебня в смеси должно быть не менее 50 % объема;
- водопоглощение щебня не должно превышать 1 %.
Результаты работы позволили также сформулировать следующие методические предложения.
- Марку по дробимости, истираемости щебня следует оценивать в водонасыщенном состоянии.
- Морозостойкость щебня показательнее оценивать в пятипроцентном растворе NaCl по ГОСТ 10060.
- Для оценки износостойкости щебня требуется комбинация методов «Лос-Анжелес» и Nord Test.
- Для определения износостойкости бетона необходимо разработать методику испытаний с техническими требованиями.
- Обеспечение свойств бетона В30, Btb 4, 0, F2300 – не является достаточной мерой для гарантии устойчивости цементобетона к образованию колеи при контакте с шипованной резиной.
Заключительные выводы рабочей группы МАДГТУ (МАДИ):
- В результате испытания цементобетонных покрытий на истираемость, установлено, что максимальную истираемость показал состав бетона (№ 5) с применением наименьших фракций щебня. Минимальную истираемость продемонстрировали составы бетонов (№ 3 и 4), изготовленные с применением порфирита фракции 5–15 мм в качестве крупного заполнителя.
- При первых 5 тыс. проходов колеса с шипованной резиной у составов бетонов, обработанных методом «щеткования», была зафиксирована наибольшая истираемость покрытий. В этот период происходит истирание растворной части, образующейся на поверхности цементобетонного покрытия при его устройстве. Наибольшую истираемость после первых 5 тыс. проходов шипованной шины показали составы бетонов (№ 6 и 7), изготовленные с применением гранитного щебня, имитирующие покрытие на М4 «Дон». На плитах (№ 6, 7) была проведена обработка поверхности свежеуложенного бетона щеткой с пластиковым ворсом. В дальнейшем износ на этих цементобетонных покрытиях замедлился.
- Как показали результаты испытаний, значительное влияние на износ цементобетонных покрытий оказывает прочность щебня и размер его фракций. Применение более прочного заполнителя и с оптимальной фракцией позволяет снизить истирание цементобетонных покрытий под действием шипованной резины в 1,5–2 раза. Строительство двухслойных цементобетонных покрытий позволяет в значительной степени сократить расход дорогостоящего щебня, применяя его только в верхнем слое покрытия.
- Используя технологию Waschbeton, можно исключить первоначальный быстрый износ бетона при сохранении требований по ровности покрытия и замедлить образование колеи в будущем благодаря удалению с поверхности покрытия слабой растворной части.
- Применение гидрофобизации цементобетонных покрытий, особенно в первые годы их эксплуатации, позволит в значительной степени укрепить поверхностный слой бетона и снизить степень разрушения от совместных воздействий противогололедных реагентов и шипованной резины.
Литература
- Износ асфальтобетонных покрытий шипованной резиной: опыт скандинавских стран [Электронный ресурс] // Dor.spb.ru : сайт группы предприятий «Дорсервис». URL: http://www.dor.spb.ru/index/technology/iznos-pokrytiy/ (дата обращения: 24.01.2020).
- Виноградов Б. Н. Влияние заполнителей на свойства бетона [Текст] / Б. Н. Виноградов. М.: Стройиздат, 1979. 223 с.
- Оценка прочности горных пород по минеральному составу: метод. указания по выполнению лабораторной работы [Текст] / сост. О. Г. Епифанцев, Н. С. Плетенчук. Новокузнецк: СибГИУ, 2007. 15 с.
- Петроченков Р. Г. Композиты на минеральных заполнителях: в 2 т. Т. 2. Проектирование составов строительных композитов: учеб. пособие [Текст]/Р. Г. Петроченков. М. : Изд-во Моск. гос. горн. ун-та, 2005. 351 с
- СП 34.13330.2012. Автомобильные дороги.
- ГОСТ 8267. Щебень и гравий из плотных горных пород для строительных работ. Технические условия.
- ГОСТ 8269. Щебень и гравий из плотных горных пород и отходов промышленного производства для строительных работ. Методы физико-математических испытаний.
- ГОСТ 8736. Песок для строительных работ. Технические условия.
- ГОСТ 10060. Бетоны. Методы определения морозостойкости.
- ГОСТ 26633. Бетоны тяжелые и мелкозернистые. Технические условия.
- ГОСТ 32703. Дороги автомобильные общего пользования. Щебень и гравий из горных пород. Технические требования.
- ГОСТ 32824-2014. Дороги автомобильные общего пользования. Песок природный. Технические требования.
- ГОСТ 33049. Дороги автомобильные общего пользования. Щебень и гравий из горных пород. Определение сопротивления дроблению и износу.
- СТБ EN 1097-9-2013. Методы определения механических и физических показателей заполнителей. Ч. 9. Определение устойчивости к истиранию шипованными шинами. Северное испытание.
- DIN EN 12620. Заполнители для бетона.